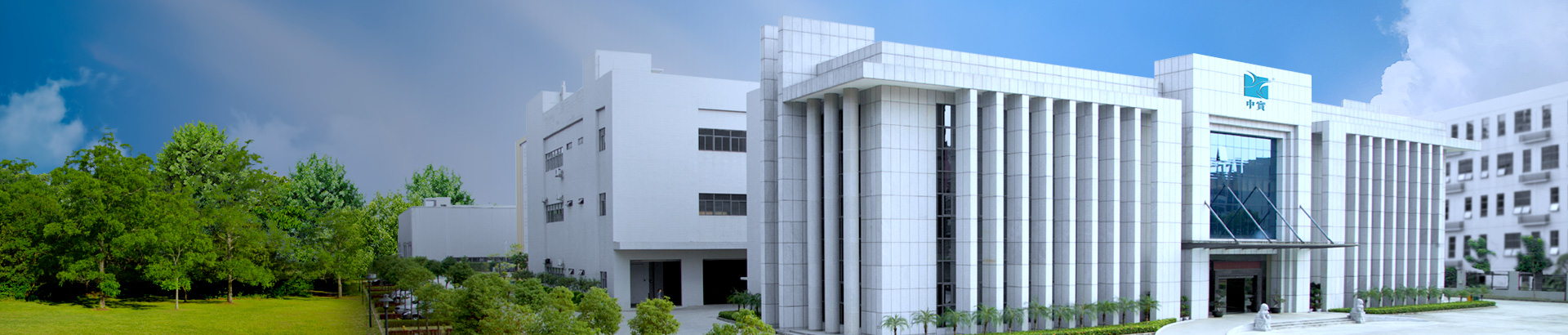
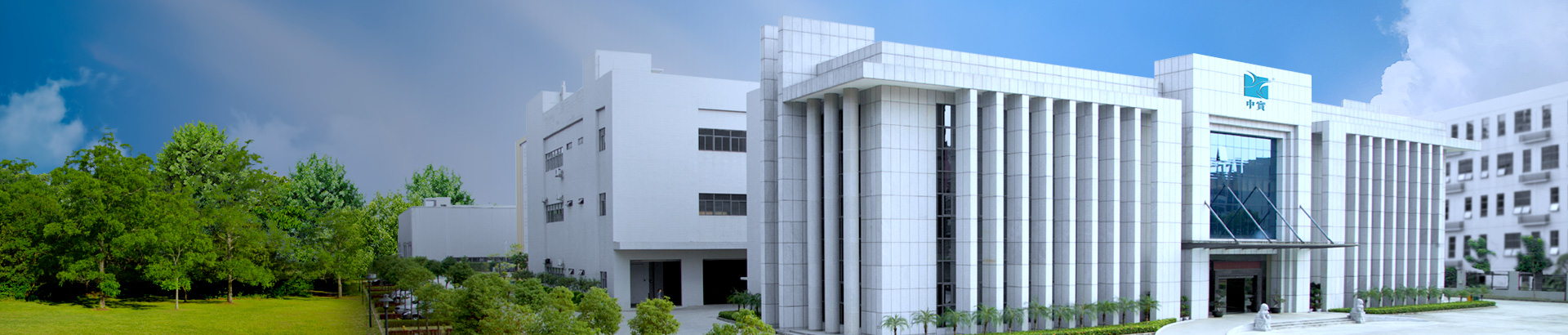
Lean Production is a method that aims to optimize manufacturing processes, improve production efficiency and reduce costs. With the intensification of market competition, more and more enterprises begin to adopt lean production to improve their competitiveness.
Since its establishment in 1999, Zhongshi Company has been trusted and recognized by more than 5000 customers because of its ultimate pursuit of product quality and considerate customer service, and has become the designated supplier of solder materials for national aerospace and military units. In recent years, with the continuous improvement of customer demand, Zhongshi has also followed the pace of customers, and constantly explore how to optimize our manufacturing process to provide better products and services.
The core idea of lean production is: based on the high-quality management of the whole process, "eliminate all waste caused by defective products" by eliminating production links that produce quality problems, pursue zero defects, and carry out continuous improvement on the existing basis. This is in line with the real quality service concept.
In March this year, under the warm invitation of Zhongshi, Mr. Qin, a senior consultant who has decades of lean production management experience and has served many state-owned enterprises, foreign enterprises and private enterprises, came to Zhongshi to create a comprehensive lean production improvement plan for Zhongshi.
Before formulating the plan, we carried out a value stream analysis, comprehensively combed the entire manufacturing process, and found the bottleneck of each link.
Then, in order to achieve the results of shortening the product delivery cycle, reducing product manufacturing costs, improving product quality and production efficiency, we formulated plans to improve the production process, eliminate waste, optimize the layout, improve the skills of employees, and began to carry out continuous improvement work.
Customer service is the core element of manufacturing enterprises, and improving customer satisfaction is also an important part of our improvement work. Through communication with customers to understand their needs and opinions, we have developed an improvement plan to meet the needs of customers to a greater extent on the basis of the original.
After more than two months of practice, Zhongshi lean production has begun to achieve results, and next, Zhongshi will continue to promote lean production improvement work, so that "lean production" from the concept to penetrate into every link and every corner of production management. Continue to output high value services for customers!
【 Lean Production Introduction 】
Fine, refers to less and fine, do not invest excess production factors, only in the appropriate time to produce the necessary amount of market urgently needed products and services (or the next process urgently needed products);
Benefit means that all production activities should be beneficial and effective and have economic benefits.
1. Value:
First of all, it is necessary to clearly and accurately define the value of our products, that is, to fully maximize the closeness to customer needs. All activities that are not consistent with customer needs are non-value-added activities, that is, waste, and need to be continuously reduced and avoided.
2. Value stream:
Having clearly defined our value, we need to connect all the processes that have value. Including: from the concept, detail design and engineering design to the whole process of problem solving tasks; Information management tasks in the whole process from receiving orders to developing detailed schedules to delivery; Material conversion tasks from raw materials to final products to end customers;
3. Flow:
Second, let all valuable and connected processes flow smoothly, completely eliminating the "waiting" and "inventory" process; The methods of relayout, streamline planning, balance and synchronization are adopted to shorten the product cycle to the maximum extent.
4. Pull:
Fully in accordance with the needs of the market and customers to reasonably arrange production and service, only when needed, according to the required quantity, production of the required products, in the absence of clear market and customer demand, can not be arranged to produce goods or provide services; Implement JIT production mode to achieve zero inventory and rapid response to market changes;
5. Get closer to perfection
Accurately define and identify each step of a specific product's value stream to introduce flows that allow end customers to pull value from its source and get products closer to their needs than ever before; At the same time, it will continue to reduce the amount of work, time, space, cost and error, and more perfect.